Realidade virtual, drones, sistemas mobiles e inteligência artificial passaram a fazer parte do dia a dia da Gerdau, desde que a empresa iniciou a implementação da Usina Virtual, projeto inspirado nos métodos da Indústria 4.0. Os resultados têm sido animadores: redução de custos, economia de energia e processos mais eficientes. Com a proposta, que teve início no final de 2015, a companhia, que é uma das principais fornecedoras de aços especiais no mundo, já registra retorno anual de R$ 15 milhões em suas unidades. A utilização de drones para monitoramento e inspeção de operações é uma das iniciativas relacionadas ao projeto. Os equipamentos sobrevoam áreas de tratamento, de transporte de material e de abastecimento, monitoram estoques de minérios e áreas administrativas, e cuidam das drenagens das águas pluviais que se direcionam para os rios. “Os drones também são usados para segurança patrimonial e de equipamentos, evitando o deslocamento de equipes pelas plantas da empresa. Na verdade, eles têm várias funções como a verificação do inventário de graneis e de sucata, inspeção de telhados e galpões, e de caixas d’água”, informa Gustavo França, gerente de TI da Gerdau.
De acordo com a empresa, as vantagens dos equipamentos são muitas: mais acuracidade nos dados e informações coletados, menos deslocamento de pessoal para execução de tarefas simples, maior rapidez nos processos e gestão mais precisa de estoques. A conferência da sucata, por exemplo, que era feita pelos funcionários anteriormente, demorava cerca de três dias; com os drones, isso é realizado em apenas sete minutos. França explica que drones também são usados para a conferência de produtos, que utilizam RFDI (Identificação por Radiofrequência).
O uso de RFDI é outra medida da Usina Virtual da Gerdau, desenvolvida para melhorar a gestão de estoques e carregamentos de caminhões na usina. Antes, ao chegar à unidade, o motorista se direcionava à portaria, realizava um cadastro, aguardava sua liberação e recebia um cartão que permitia a sua entrada. Dentro da usina, ao passar pela balança, o caminhoneiro era direcionado à área de carregamento de perfis estruturais. Na sequência, ele seguia para o carregamento do produto, onde seu veículo aguardava até que um colaborador da companhia liberasse o carregamento, que era identificado de forma manual no estoque.
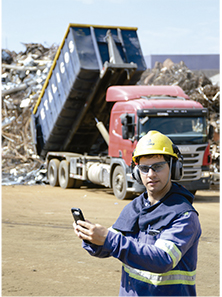
A implantação do RFID criou um ambiente de rastreabilidade automática para as movimentações de produtos e equipamentos, com foco na automação dos processos de recebimento, gestão de estoques e carregamentos. Foram instalados diversos sensores e leitores de RFID nos equipamentos de movimentação interna na usina, como pontes rolantes e empilhadeiras. O processo contribui para que o colaborador coordene o sistema de carregamento dos caminhões de forma automática, direcionando onde serão coletados os materiais que ficam no estoque. “O sistema permite a conectividade entre os produtos, os clientes e os colaboradores, proporcionando mais rapidez e eficiência. Os drones podem fazer a leitura do RFDI, mesmo naqueles produtos que estão mais escondidos. Não há mais necessidade de que isso seja feito manualmente. O inventário de estoques, que chegava a demorar 30 dias, agora é realizado em menos de 30 minutos”, afirma.
O sistema RFDI permite o rastreamento da mercadoria até o cliente, dando mais transparência ao processo, inclusive melhorando as rotas e garantindo segurança e produtividade. “Na Gerdau, não medimos esforços quando falamos de inovação e digitalização na indústria do aço. Em linha com um dos principais valores da companhia, a iniciativa garante o aprimoramento da gestão dos equipamentos e estoques, garantindo um ganho de produtividade nas operações logísticas, e contribuindo também para que nossos clientes acompanhem em tempo real o rastreamento de sua mercadoria, desde a saída da usina até o destino final”, destaca Carlos Hamilton, diretor industrial da Usina Ouro Branco.
Leia mais na revista na revista Transporte Moderno nº482 no Acervo Digital OTM